Przez szczeliny wydmuchowe jednocześnie z parą wylotową odpływa, lub też zostaje porwana przez wchodzącą parę, znaczna ilość oleju smarnego. Przy nastawieniu dopływu oleju do cylindrów maszyn przelotowych należy wziąć to pod uwagę. Sposoby doprowadzania smaru dla tych maszyn nie różnią się od sposobów opisanych na początku dla maszyn nie przelotowych ( zmiennoprądowych ). Najczęściej jednak bywa stosowane w maszynach przelotowych bezpośrednie doprowadzanie smarów.
Pokrywy cylindrów maszyn przelotowych są ogrzewane parą. W maszynach zamkniętych ( obudowanych ) pokrywy cylindrów mogą osiągnąć temperaturę tak wysoką, że rozpryskiwany przez mechanizm korbowy olej maszynowy, opadający na te pokrywy, zostaje odparowany. To parowanie może występować w tak silnym stopniu, iż oprócz większego rozchodu smarów, powstające dymy dają się we znaki obsłudze maszyny i mogą wywołać przeszkody w ruchu ustawionych w hali maszyn elektrycznych. Poleca się umieszczenie przykrywki ochronnej z dławicą dodatkową przed właściwą pokrywą cylindra. Dławnica dodatkowa posiada zgarniacze pierścieniowe, które nie dopuszczają oleju maszynowego, porywanego przez drąg tłokowy do gorącej dławnicy głównej, gdzie olej mógłby parować. Należy nadto zauważyć, iż przy silniejszym rozbryzgiwaniu oleju maszynowego, porywanego przez mechanizm ruchu olej ten w wypadku niezastosowania opisanego urządzenia ochronnego może zostać wciągnięty w tak znacznej ilości do dławnicy głównej, iż możliwe są poważne uszkodzenia tejże, jeżeli pominiemy milczeniem duży rozruch smaru.
W wypadkach takich należy do smarowania mechanizmu ruchu używać oleju maszynowego bardzo gęstego, trudniej parującego. Na zmniejszenie parowania smaru korzystnie wpływa prawidłowe nastawienie doprowadzania oleju do mechanizmu ruchu, tak aby ilość tego oleju była jak najmniejsza. Warunki podobne mogą powstawać i w maszynach nieprzelotnych ( zmiennoprądowych ), skoro te ostatnie posiadają ogrzewane pokrywy cylindrów.
Na rysunku 14 widzimy leżącą maszynę parową przelotową, które części główne zostały przedstawione w przekroju pionowym; linie czerwone wskazują schematycznie układ doprowadzanie smaru. lej maszynowy jest tłoczony przez smarownicę mechaniczną a i dopływa pod ciśnieniem do poszczególnych miejsc, wymagających smarowania. W ten sposób olej zostaje doprowadzony pod ciśnieniem do łożysk wału korbowego, do wodzika i smarownicy, dławnic, drąga tłokowego oraz do czopu korbowego. Ta sama tłocząca smarownica mechaniczna a, napędzana do wałka stawidłowego, doprowadza olej do cylindra oraz do dławic. Smarownica tłoczy olej do dławnic oraz do rozpylaczy smaru, które są wbudowane w kosze zaworów wpustowych. Olej cylindrowy zostaje rozpylony i porwany przez dopływającą parę.
W ten sposób wszystkie części wewnętrzne posiadają równomierny dopływ oleju. Jest to nader ważne zwłaszcza dla długiego i ciężkiego tłoka, gdyż od właściwego smarowania tego ostatniego zależy gładki i bez przeszkód bieg maszyny. Olej i skropliny spływają z dławnic do żłobu zbiorczego, znajdującego się między pokrywą cylindra a dławicą dodatkową, skąd są odprowadzane, zaś olej z łożysk zbiera się w żłobie podkorbowym i przed dławnicą dodatkową.
.png) |
Cylinder maszyny przelotowej ( równo-prądowej ) |
A - Tłok i pierścienie tłokowe, B - Drąg tłokowy, C - Cylinder, D - Pokrywa cylindra, E - Otwór wlotowy dla pary, F - Zawory wlotowe, G - Otwór wylotowy, H - Nasadka dla wylotu pary, J- Zawór do włączenia dodatkowej przestrzeni szkodliwej, K - Dławnica główna z doprowadzaniem oleju, L - Dławnica dodatkowa ze spustem do odprowadzania oleju, M- Otwór do odprowadzania powietrza z komory między dławnicami główną a dodatkową, N - Spust do oleju cylindrowego, O - Spust dla oleju do smarowania mechanizmu korbowego, P - Krzyżulec, Q- Prowadnica, R - Doprowadzanie oleju do cylindra.Rodzaje stawideł
Stawidłami nazywamy mechanizmy, które otwierają i zamykają kanały parowe, uskuteczniając rozrząd pary. Stawidła, używane najczęściej, są następujące :
- stawidło z suwakiem płaskim
- stawidło z suwakiem tłokowym
- stawidło z podwójnym suwakiem tłokowym
- stawidło z suwakami kruczkowymi Corlissa
- stawidło zaworowe
Rodzaj stawidła wywiera wpływ na smarowanie maszyny parowej, gdyż od niego zależny jest sposób prowadzenia pary i szybkość jej przelotu, oraz obciążenie i kształt tych powierzchni stawidłowych, które wymagają smarowania. Skoro więc zmieniają się warunki ruchu i dopływu pary przy danej budowie stawidła, to zmieniają się zwykle wymagania, stawiane smarowaniu. Ponieważ stawidła są w ocenie działania maszyny parowej czynnikiem niezmiernie ważnym, podamy tutaj krótki opis głównych systemów rozrządu. Z zestawienia poniższego wynika, iż zwykłe stawidła z suwakami płaskimi, podwójnymi suwakami tłokowymi i stawidła Corlissa znajdują zastosowanie tylko przy niskich temperaturach pary, niewielkich ciśnieniach i ilościach obrotów, natomiast stawidła z suwakami tłokowymi i zaworowe, odpowiednie są dla wysokich temperatur pary, dużych prężności i wielkiej ilości obrotów oraz dużych mocy.
 |
Dane, dotyczące różnych stawideł |
Stawidło z suwakiem płaskim
Rozrząd z suwakiem płaskim - to najdawniejsza budowa stawidła. Na rysunku 16 przedstawiony został suwak płaski, spoczywający na kształt muszli na gładzi suwakowej i zamknięty w skrzynce suwakowej. Dla zrozumienia rysunku przedmioty są ustawione tak, jak gdyby były na wpół przezroczyste. Suwak sunie po gładzi suwakowej, która tworzy nadlew na cylindrze i jest dociskany przez prężność pary do gładzi, gdyż para świeża wywiera na cześć górną suwaka muszlowego H ciśnienie znacznie większe, niż para wydmuchowa w A i C. Widzimy więc, że zwykły suwak płaski nie jest odciążony. Gładź suwakowa musi być obrobiona zupełnie gładko i dokładnie w jednej płaszczyźnie; przez kanały łączy się ona z wnętrzem cylindra. Obieg pary odbywa się w porządku ponumerowanych strzałek. Para świeża dopływa przez rurę wlotową ( 1 ) i przy położeniu suwaka, widocznym na rysunku, wlatuje przez kanał lewy ( 2 ) i oddaje pracę, przesuwając tłok na prawo. Para ta dopływa tak długo, dopóki tłok nie wykona 1/3 swego suwu na prawo.
Mówi się wówczas, że napełnienie wynosi 1/3. Następnie suwak zamyka krawędzią sterującą wlot, zaś para rozprężając się ( ekspansja ) przesuwa tłok dalej. Para już rozprężona po drugiej stronie tłoka płynie przez kanał prawy ( 4 ) i po stronie wewnętrznej suwaka muszlowego ( 5 ), następnie przez rurę wydmuchową ( 6 ) i ( 7 ) na zewnątrz lub do skraplacza. Ponieważ droga przepływu pary ze względu na skraplanie i spadek prężności winna być możliwie krótka, w szczególności zaś aby " przestrzeń szkodliwa " była jak najmniejsza, cylinder wykonany bywa w jednym odlewie z gładzią suwakową. Suwak H złączony jest z drążkiem suwakowym B i napędzany jest od wału korbowego za pomocą mimośrodu, przy czym suwak otrzymuje za pomocą mimośrodu i drążka mimośrodu taki ruch od wału korbowego, że otwieranie i zamykanie kanałów parowych następuje we właściwym czasie, zgodnie z zamierzonym rozdziałem pary według wykresu indykatora.
Wadą suwaka płaskiego są duże powierzchnie cierne, co wymaga większego nakładu pracy, niż do napędu innych narządów stawidłowych. Straty te zwiększają się jeszcze znacznie, gdy suwak nie jest odciążony tzn. gdy nacisk pary na suwak jest jednostronny. Szczelność suwaka jest również nie jest tak zupełna, jak przy użyciu suwaków tłokowych, które będą opisane później tak, że w rezultacie otrzymujemy cokolwiek większy rozchód pary. Suwaki płaskie nie są tak odporne na wysokie prężności pary, jak inne suwaki, gdyż nawet przy najlepszemu smarowaniu istnieje możliwość zacierania się suwaka. Przy zastosowaniu pary silnie przegrzanej suwaki te " paczą się " łatwo, co znowu ułatwia zacieranie się suwaków, pomijając powstające już przez to straty pary.
Dalszą wadą suwaka płaskiego jest, iż otwiera się on zbyt powolnie kanał wlotowy pary. Stąd duże dławienie pary przez bardzo wąską szczelinę 2, a straty dławienia wyrażają się w spadku prężności i zmniejszonej sprawności. Ze zmianą napełnienia przy zmiennym obciążeniu połączona jest przy suwakach płaskich zmiana wlotu przed zwrotowego i sprężania, gdyż te punkty charakterystyczne zależne są od przymusowego ruchu suwaka. Stąd dalsza strata pracy i wada tego stawidła. Ulepszeniem zwykłego suwaka płaskiego jest suwak Tricka. Kanał przelotowy umożliwia dopływ jednoczesny pary przez dwa otwory, a więc podwójnie szybko, co oznacza zmniejszenie straty dławienia przy otwieraniu i zamykaniu. Zwykły suwak płaski przedstawiony na rysunku 16, może być więc bardzo ulepszony przez odciążenie gładzi suwakowej, zaś z drugiej strony przez kanał przelotowy, umożliwiający szybsze napełnianie cylindra.
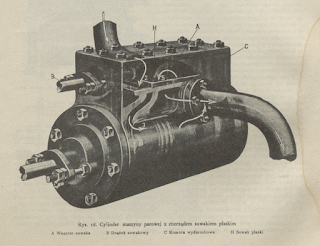 |
Cylinder maszyny parowej z rozrządem suwakiem płaskim |
A - Wnętrze suwaka, B - Drążek suwakowy, C - Komora wydmuchowa, H - Suwak płaski.
Stawidło z suwakami tłokowymi
Rozrząd suwakami tłokowymi odbywa się za pomocą krawędzi sterujących dwóch tłoków żeliwnych E. Mimośród wraz z drążkiem suwakowym K nadaje, jak w zwykłym suwaku płaskim, suwakowi tłokowemu ruch posuwisty z niewielkim wyprzedzeniem w stosunku do ruchu tłoka w cylindrze roboczym - w metalowej tulei B, która w ściankach posiada otwory D dla wlotu i wylotu pary. Otwory w tulei są dostosowane do szerokości kanałów wlotowych i wylotowych, tak że para spotyka wszędzie ten sam przekrój przelotowy, nie ma więc dławienia pary, ani spadku prężności. W maszynach na parę nasyconą i dla niskich prężności pary tłok zostaje obrobiony tak, że pasuje dobrze do tulei, co daje szczelność wystarczającą.
Dla maszyn na parę przegrzaną i zwłaszcza na prężności wyższe takie uszczelnienie nie jest wystarczające i oba tłoki E otrzymują, podobnie jak tłoki robocze, pierścienie uszczelniające G, które zapewniają większą szczelność.
 |
Cylinder maszyny parowej, sterowany przez suwak tłokowy |
B - Tuleja suwaka, D - Kanał wlotowy, E - Suwak tłokowy, K - Drążek suwakowy, F - Okienko wlotowe, G - Pierścienie suwaka tłokowego, J - Komora wewnętrzna suwaka, R - Komora wydechowa
W widocznym na rysunku położeniu suwaka tłokowego para dopływa z rury, doprowadzającą parę świeżą F, przez część środkową tulei suwaka tłokowego do prawego kanału w kierunku oznaczonym przez strzałki białe. Jednocześnie para wydmuchowa z poprzedniego suwu zostaje usunięta przez kanał lewy, otwory w części lewej suwaka tłokowego i przewód wydmuchowy, płynąc w kierunku odnośnych strzałek. Przebieg roboczy jest zatem taki sam, jak u suwaka zwykłego. Mówimy, że wlot jest wewnętrzny, gdy para świeża znajduje się wewnątrz narządu sterującego w komorze J, a na zewnątrz tego w komorze R znajduje się para odlotowa. Przy wlocie tak zwanym zewnętrznym warunki są odwrotne. Wlot wewnętrzny, w przeciwieństwie do wlotu zewnętrznego, powoduje mniejsze ochładzanie pary, a co za tym idzie mniejsze skraplanie wlotowe i zwiększoną sprawność silnika.
Wlot wewnętrzny ma dalej tę zaletę, iż dławnice drążków suwakowych są szczelniejsze, gdyż znajdują się tylko pod działaniem pary o ciśnieniu wylotowym, zaś skrzynka suwakowa nie jest otoczona na całej swojej powierzchni przez parę świeżą. Dzięki temu zmniejszają się z jednej strony straty ciepła przez promieniowanie, z drugiej strony unika się jednostronnego rozszerzania się pod wpływem ciepła i możliwych pęknięć cylindrów.
Z ustroju suwaka tłokowego wynika, iż jest on całkowicie odciążony ( w przeciwieństwie do suwaka płaskiego ), co ułatwia skuteczne smarowanie. Wobec znacznie mniejszego ciężaru suwaka tłokowego występują przy wielkiej ilości obrotów mniejsze siły masowe, co zapewnia spokojniejszy bieg silnika. Specjalną zaletą suwaka tłokowego jest więc, iż może on być użyty przy zastosowaniu pary o wysokim przegrzaniu, nawet do 400 stopni C. i więcej. Nie należy również obawiać się " paczenia się " tego suwaka pod wpływem wysokiej temperatury.
Wobec możliwości stosowania tego stawidła przy wysokich temperaturach pary i dużych ciśnieniach, bez poważniejszych stron ujemnych, z wyjątkiem tej wady, że zmiana napełnienia powoduje zmianę charakterystycznych punktów rozrządu pary, jak to zostało omówione przy suwaku płaskim, stawidła z suwakiem tłokowym są stosowane ogólnie w parowozach na kolejach normalnotorowych, które to maszyny należą do najbardziej obciążonych silników parowych.
Z wyżej przytoczonych przyczyn w silnikach, poruszanych parą, o wysokich prężnościach i przegrzaniu, znajdujemy ogólnie układ przedstawiony na rysunku 17, a więc wlot wewnętrzny i dławnicę drążka suwakowego, na która działa tylko para odlotowa o niskim ciśnieniu pary nasyconej.
Za odmianę suwaka tłokowego można uważać stawidło dyfuzorowe według patentu prof. Guttermutha. Kanały wlotowe pary w stawidle tym wykonane są w kształcie dysz, dzięki czemu suwak tłokowy o średnicy bardzo małej bez pierścieni uszczelniających daje wystarczający rozrząd pary bez żadnych strat dławienia. Zaletą tego stawidła jest bardzo lekka budowa wszystkich części stawidła, gdyż masy ruchome są bardzo niewielkie, oraz nieznaczne ścieranie się części wobec bardzo niewielkich ciśnień powierzchniowych w czasie biegu.
Stawidło z suwakiem tłokowym dwoistym
Inny rodzaj stawidła suwakowego został przedstawiony na rysunku 18, a mianowicie stawidło z suwakiem tłokowym dwoistym. Obydwa suwaki są wykonane jako suwaki tłokowe. Przy zastosowaniu zwykłych suwaków płaskich i tłokowych ze zmianą napełnienia przez regulator jest połączona szkodliwa zmiana pozostałych punktów charakterystycznych wykresu ( wlot przed zwrotowy, wylot przed zwrotowy, sprężanie ). W omawianym stawidle usunięto tą wadę w ten sposób, iż zamknięcie kanałów wlotowych pary odbywa się za pomocą oddzielnego suwaka.
Suwak rozdzielczy G ma wycięcie normalne F takie jak opisane w poprzednio w stawidle z suwakiem tłokowym. W suwaku rozdzielczym G porusza się mimośrodowo suwak ekspresyjny E. Dla zmniejszenia tarcia oba suwaki poruszają się w tulejach brązowych, suwak rozdzielaczy w tulei L, suwak ekspansyjny w tulei D. Ten ostatni suwak posiada skośne wycięcia A. Może on oprócz ruchu naprzód i wstecz wykonywać jednocześnie ruch obrotowy.
Drążek suwaka ekspansyjnego jest bowiem poruszany naprzód i wstecz przez tak zwany mimośród ekspansyjny i jednocześnie może być obracany za pomocą zębatki J i kółka zębatego K. Takie same skośne wycięcia znajdują się w tulei D, połączonej z suwakiem rozdzielczym G przez śruby N. Dopóki wycięcia A i B pokrywają się wzajemnie, zaś z drugiej strony otwory F w suwaku tłokowym dają wolny dostęp do kanału wlotowego dla pary M, para świeża może dopływać.
Gdy obciążenie maszyny wzrasta, tak, że ilość obrotów spada, regulator porusza zębatkę J i obraca z pomocą kółka zębatego K suwak ekspansyjny w ten sposób, iż teraz wycięcia A i B w czasie swojego biegu naprzód i wstecz pozostają w dłuższej łączności ze sobą, dzięki czemu napełnienie S1 zostaje powiększone.
 |
Cylinder maszyny parowej ze stawidłem o podwójnym suwaku tłokowym |
A - Okienka w suwaku ekspansyjnym, B - Kanał wlotowy w tulei suwaka, D - Tuleja suwaka ekspansyjnego, E - Suwak ekspansyjny, F - Kanał wlotowy w suwaku rozdzielczym, G - Suwak rozdzielczy, H - Drążek suwaka ekspansyjnego, J - Zębatka do przesuwania suwaka ekspansyjnego, K - Kółko zębate do przestawiania suwaka ekspansyjnego, L - Tuleja suwaka ekspansyjnego, M - Kanał parowy, N - Śruby, łączące tuleję suwaka z suwakiem rozdzielczym.
Opisane powyżej stawidła z suwakiem tłokowym dwoistym do zmiany napełnienia bez zmian pozostałych punktów wykresu, są oczywiście bardzo skomplikowane i stawały się niejednokrotnie przyczyną zakłóceń ruchu, zwłaszcza przy rozwijaniu większych mocy.
Stawidło kruczkowe Corlissa
Za znacznie ulepszone w porównaniu do zwykłego, nieodciążonego suwaka płaskiego bez kanału przelotowego, musi być uważane stawidło kruczkowe lub kurkowe Amerykanina Corlissa. Zaletą tego stawidła jest, iż kanały wlotowe i odlotowe mogą być bardzo krótkie, dzięki czemu osiąga się bardzo nieznaczne skraplanie wlotowe, oraz zmniejszenie przestrzeni szkodliwej. Następnie można prostymi środkami tak zmieniać mechanizm napędowy kurków Corlissa, iż zwiększa się lub zmniejsza napełnienie, nie zmieniając przez to wlotu przed zwrotowego i kompresji, o co zawsze należy się starać przy zmianie napełnienia.
Mimo pewnych zalet suwaki Corlissa dzisiaj prawie całkowicie wyszły z użycia i spotyka się w w silnikach starszych konstrukcji. Wadą tego stawidła jest, iż suwaki Corrlisa z biegem czasu stają się nie szczelne. Przyczyną tego jest nader trudne utrzymanie warstewki smaru na ślizgających się po sobie powierzchniach, zwłaszcza przy pracy z parą przegrzaną.
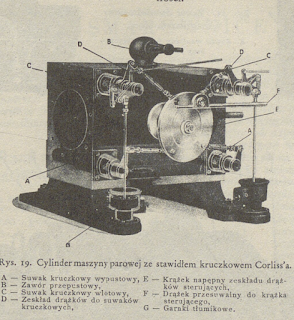 |
Cylinder maszyny parowej ze stawidłem kruczkowym Corlissa |
A - Suwak kroczkowy wypustowy, B - Zawór przepustowy, C - Suwak kruczkowy wlotowy, D - Zeskład drążków do suwaków kruczkowych, E - Krążek napepny zeskładu drążków sterujących, F - Drążek przesuwalny do drążka sterującego, G - Garnki tłumikowe.
Stawidło zaworowe
W czasach obecnych stosuje się ogólnie stawidło zaworowe, które dają doskonały rozrząd pary, również i przy silne zmiennym obciążeniu. Każdy zawór ma napęd oddzielny, nie zależny od napędów innych zaworów, co jest jedną z główniejszych zalet stawidła zaworowego, gdyż zmiana napełnia przez regulator nie pociąga za sobą zmiany pozostałych punktów charakterystycznych wykresu.
Zawory ( wentyle ) - mogą być wykonane, jako zawory tłokowe lub jako zawory jedno i wielosiedzeniowe. Nazwa bierze się stąd, iż zawór siedzi na dwóch siodłach; uwidoczniony przez końce strzałek. Para przepływa zarówno przez zawór, jak między kadłubem zaworowym, a siodłem górnym zaworu.
Zawór tłokowy - to właściwie suwak tłokowy z pierścieniami uszczelniającymi, umieszczony w skrzynce zaworowej. Jest on całkowicie odciążony i posiada najmniejszą przestrzeń szkodliwą. Poza tym posiada on zalety suwaka, bieg spokojny i bez wstrząśnień, oraz korzystne warunki ruchu:
Stawidła zaworowe spotykamy prawie wyłącznie w maszynach leżących. Zawory umieszczone są na końcach cylindra, a mianowicie: dwa zawory wlotowe, otwierające się zawsze na zewnątrz, zwykle u góry, po jednym na każdym końcu, oraz dwa zawory wylotowe, otwierające się stale na zewnątrz, u dołu. Umożliwia to łatwe spływanie skroplin, powstających w cylindrze podczas rozruchu. Zawór w położeniu zamkniętym powinien być dociskany do swego gniazda przez prężność pary, co zabezpiecza szczelność zamknięcia.
Równolegle do osi cylindra umieszczony jest wałek rozrządczy, napędzany przez parę kół zębatych od wału korbowego. Napęd zaworów może być osiągnięty różnymi sposobami. W naszym wypadku na wałku rozrządczym L osadzony jest mimośród M, który za pomocą drążka mimośrodowego N, dźwigni wahadłowej O wraz z rolką sprawia, iż trzon zaworu podnosi się i opuszcza.
Zawory jedno i wielosiedzeniowe mogą być tak napędzane, iż ruch zaworu jest całkowicie przymusowy, lub też tak, że zamykanie odbywa się z wolnym spadkiem. W tym pierwszym wypadku zawór połączony jest stale z mechanizmem napędowym, zarówno podczas otwierania, jak i zamykania zaworu. W zaworach z wolnym spadem jedynie odmykanie zaworów jest przymusowe, podczas gdy zamykanie uskuteczniane jest przez sprężynę.
Co się tyczy smarowania, to godnym uwagi jest stawidło Lentza, jakie spotykamy w Lokomobilach stałych. W stawidle tym są otwierane i zamykane zawory, umieszczono poziomo, za pomocą wałka palczastego, który napędzany jest ruchem wahadłowym od wału głównego za pośrednictwem mimośrodu, drążka mimośrodowego i krótkich, jednoramiennych dźwigienek. Wałek palczasty umieszczony jest w kanale sterującym, wykonanym jako kąpiel olejowa i stale wystawiony na wysoką temperaturę pary.
Nieodpowiednie smary powodują powstawanie osadów na trzonach zaworowych i wałku palczastym i, co za tym idzie znaczne zakłócenia niewielkich skoków tych narządów sterujących. Osobny rodzaj zaworów - to zawory sterowane parą. Działanie tych zaworów jest następujące :
W punkcie martwym maszyny zawór jest otwarty pod działaniem sprężania. W komorze nad zaworem utrzymywane jest niższe ciśnienie, niż w skrzynce wlotowej dla pary cylindra roboczego. Para dopływa do cylindra przez szczelinę. Ponieważ szczelina ta jest stosunkowo mała, powstaje na wskutek zwiększającej się chyżości tłoka we wnętrzu cylindra, a więc i pod zaworami, nieznaczne podciśnienie, wywołane przez dławienie. Skoro ciśnienie nad zaworem przewyższy ciśnienie pod zaworem, ten ostatni zostaje zamknięty.
W wykonaniu zaworom tym nadaje się możliwie najmniejszą masę i bardzo mały skok - około 1 mm, co podnosi pewność ich działania. Oczywiście zawory te mogą być przestawione również przez zwykły regulator.
Dławnice
Dławnice zamykają i uszczelniają cylindry w miejscu przenikania drągów tłokowych i drążków suwaków. Co się tyczy szczeliwa rozróżniamy szczeliwo miękkie i metalowe. Każda dławnica posiada kadłub A, szczeliwo D oraz dławik B, dociskany przez śruby. Ponieważ ugięcie drąga tłokowego stale się zmienia, należy więc w celu zapobieżenia szybkiemu ścieraniu się dławnic stosować szczeliwa ruchome.
 |
Dławnice |
Rys 23a, szczeliwo miękkieRys 23b, szczeliwo metalowe
Rys 23c, szczeliwo metalowe ze sprężynami pierścieniowymi
A - Kadłub, B - Przeciwdławik, C- Szczeliwo miękkie, D - Pierścienie uszczelniające, E - Żłobki, F - Sprężyny pierścieniowe
Szczeliwa miękkie
Szczeliwo to jest używane na ogół tylko przy pracy parą nasyconą o stosunkowo niższej prężności. Zwykłe tarcie pomiędzy szczeliwem, a drągiem tłokowym jest stosunkowo duże, zaś przy zbyt mocnym dokręceniu śrub dławnic tarcie te może zwiększyć się, iż następuje nadmierne ścieranie, a w związku z tym ciągłe straty pary. Przede wszystkim należy zwracać szczególną uwagę na równomierne dokręcenie śrub dławnic. Szczeliwo miękkie sporządzone jest z tkaniny azbestowej lub z azbestowo-bawełnianej, często w wkładką gumową.
Szczeliwo metalowe
Szczeliwa metalowe przy wysokich temperaturach pary są znacznie odpowiedniejsze od szczeliw miękkich. Muszą one być samonastawne, ażeby ugięcie się drąga tłokowego nie wywołało zacięcie się drąga w szczeliwie, gdyż w wyniku otrzymalibyśmy wyciśnięcie warstwy smaru, a co za tym idzie tarcie metaliczne ze wszystkimi skutkami. Na rysunku 23 b, przedstawione jest szczeliwo metalowe, którego działanie doszczelniające po dokręceniu śrub polega na tym, iż skośne ścięte pierścienie brązowe o trójkątnym przekroju zostają dociśnięte do drąga tłokowego. Żłobki E, wywołują skraplanie pary i ułatwiają poza tym smarowanie dławic. Pierścienie uszczelniające powinny tylko z lekka naciskać drąg tłokowy.
Na rysunku 23c przedstawione zostało szczeliwo metalowe, używane często w maszynach parowych. W tym wypadku dociskanie metalowych pierścieni uszczelniających D do drąga tłokowego, odbywa się pod działaniem sprężyn pierścieniowych. W tym czasie, gdy stosowanie pary wysoko przegrzanej i wysokoprężnej zaczęło wchodzić w użycie, nienaganne wykonanie uszczelnień sprawiało wiele trudności, ponieważ dawna forma wykonania - szczeliwo miękkie - zawodziła, przy wysokich temperaturach i ciśnieniu. Dopiero wprowadzeniu szczeliw metalowych w odpowiednim wykonaniu całkowicie usunęło tą trudność.
Smarownice
Na ogół rozróżniamy dwa rodzaje przyrządów do smarowania cylindrów maszyn parowych :
- smarownice napędzane mechanicznie
- smarownice napędzane hydrostatycznie
Najszersze zastosowanie mają z pośród nich, te pierwsze w postaci mechanicznych smarownic z wziernikami lub w postaci pras systemu Mollerupa.
Mechanicznie poruszana smarownica
Najpewniej pracują smarownice napędzane mechanicznie, gdyż doprowadzają one olej przymusowo pod określonym ciśnieniem. Jedną z najlepszych smarownic jest mechaniczna smarownica Delvaca ( Rys. 14 ), która w zależności od zapotrzebowania posiada o 1 do 16 przewodów doprowadzających olej do miejsc smarowanych. Smarownica ta może być zastosowana do napędów wszelkiego rodzaju, jak napęd dźwignią, zapadką, ślimacznicą, oraz rolkowym mechanizmem zapadkowym. Przy ciśnieniach niższych do 30 atmosfer stosuje się wzierniki w formie tzw. " bulleye ", czyli " wolich oczu ". Wzierniki te umożliwiają dokładnie sprawdzanie doprowadzonej w każdej chwili ilości oleju, przez obserwowanie pojawiających się w zierniku kropelek oleju.
Smarownica tłocząca ( Prasa Mollerupa )
Prasy smarownicze Mollerupa ( Rys. 25 ), są bardzo często stosowane w maszynach parowych. Dzwignia H otrzymuje napęd od jakichkolwiek części maszyny parowej o ruchu posuwistym, przy czym przy każdym skoku naprzód zapadka A, wciska się między zęby koła zapadkowego B. Za pomocą ślimaka i ślimacznicy tłok K porusza się w naczyniu cylindrycznym bardzo wolno ku dołowi i tłoczy w ten sposób olej smarny znajdujący się w zbiorniku przez przewód L, do miejsc smarowanych. Po wyciągnięciu sworznia D, w celu odłączenia korby od napędu ślimakowego i po wykręceniu z powrotem wrzeciona za pomocą korby C, prasę napełnia się na nowo.
W danym wypadku za pomocą kurka zmianowego ( wielodrogowego ) W i naczynia do oleju V ( L - spust oleju ) napełnianie może nastąpić już podczas skoku w górę tłoka. Ażeby zapobiec obracaniu się tłoka w dławnicy bez poruszania się w górę i dół, przewidziany jest ząb przykładowy F, przylegający do jednego z obu słupków. Korbka ręczna C służy następnie do tego, aby przy przejściowo zwiększonym zapotrzebowaniu oleju szybciej poruszać na dół tłok i w ten sposób zwiększać ilość doprowadzonego oleju.
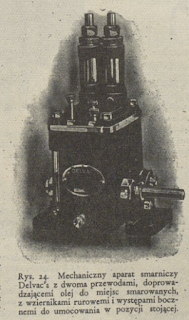 |
Mechaniczny aparat smarniczy Delvaca z dwoma przewodami, doprowadzający olej do miejsc smarowanych, z wziernikami rurowymi i występami bocznymi do umocowania w pozycji stojącej |
Oliwiarka hydrostatyczna
W oliwiarce tej ciśnienie pary wraz z działaniem hydrostatycznym skroplin, oraz różnicy ciężarów właściwych, służy do doprowadzenia oleju do miejsc smarowanych. Rurka A ( patrz rys 26 ) jest włączona do przewodu parowego i płynie nią para, która częściowo skrapla się już przez ochłodzenie w kulistej komorze kondensacyjnej K. Odcinek rury ponad komorą K. musi mieć co najmniej 650 mm wysokości, aby wytworzyć wystarczający słup wody do tłoczenia z całą pewnością oleju przez oliwiarkę. Od komory kondensacyjnej prowadzi przewód odwadniający B prawie do dna zbiornika C. Wobec różnicy ciężarów właściwych olej zbiera się nad wodą. Olej wlewa się przez otwór do napełnienia, zamykany przez nakrętkę S i zostaje doprowadzony przez rurkę F do dyszy D. W zależności od zapotrzebowania smaru można za pomocą zaworu E, regulować lub zupełnie zamknąć dopływ oleju.
Olej wypływa przez dyszę D, przy czym wznoszące się ku górze krople są widoczne w wzierniku T, zbiera się u góry i przez rurkę G zostaje rozprowadzony do miejsc smarowanych. Woda we wzierniku T nie łączy się z wodą na dnie zbiornika C. Wypływ oleju z dyszy D, regulowany przez zawór E, odbywa się więc pod działaniem stale rosnącej skroplin, które olej unoszą do góry i w ten sposób wypierają. Dla przerwy w smarowaniu zamyka się przewód parowy A i olejowy G przez zawory J i H, podczas gdy zawór regulujący E. pozostanie w położeniu niezmienionym. W zależności doprowadzonego oleju poziom wody w zbiorniku C podnosi się. Należy pamięta o dolewaniu oleju na czas, zanim poziom wody osiągnie poziom rurki doprowadzającej olej F, co jest widoczne przez szkło olejowskazu O.
Po odkręceniu korków gwintowanych ma się dostęp do wszystkich części przyrządów dla czyszczenia ich. Zawartość zbiornika C można spuścić przez kurek spustowy L. Ilość doprowadzonego oleju zależna jest również od zmiany ciekłości oleju w różnych temperaturach. Przy ponownym napełnianiu olejem mogą powstać nieprawidłowości przy nie umiejętnym obchodzeniu się z oliwiarką.
 |
Smarownica tłocząca - oliwiarka hydrostatyczna |
Smarownica tłocząca: A - Zapadka, B - Koło zapadkowe, C - Korbka ręczna, D - Wstrzymnik, E - Cylinder prasy, F- Ząb przykładowy, H - Dźwignia napędowa, K - Tłok prasy, L - Spust oleju, V - Naczynie do oleju, W - Kurek wieloprzelotowy.
Oliwiarka hydrostatyczna: A - Rurka dopływowa pary, B - Rurka do skroplin, C - Zbiornik oleju, D - Dysza, E - Zawór, F - Rurka doprowadzająca olej, G - Przewód oleju, H i J - Zawory regulacyjne, K - Skraplacz, L - Kurek spustowy, O - Olejowskaz, S - Korek do napełnienia, T - Wziernik, W - Zwierciadło wody.
Sposoby doprowadzania oleju
Sposób doprowadzania oleju ma często wpływ na dobroć smarowania, dlatego należy omówić różne w tym celu stosowane systemy. Smar do cylindra i wewnętrznych narządów rozrządczych może być doprowadzany sposobami następującymi :
- do skrzynki stawidłowej
- wprost do cylindra
- bezpośrednio do głównego przewodu pary
Doprowadzanie oleju do skrzynki stawidłowej
W stawidłach z suwakiem płaskim olej bywa doprowadzany zwykle do skrzynki suwaka, gdzie zostaje porwany przez strumień pary i rozprowadzony. Przez kanały rozrządcze smar zostaje doprowadzony do wnętrza cylindra. Skutkiem takiego doprowadzenia smaru było częste osadzenie się oleju i powstanie oskorupień w kątach komór cylindrowych i suwakowych. Stosowanie suwaków płaskich zostało na ogół dzisiaj zarzucone. W stawidłach z kurkami Corlissa olej bywa zwykle doprowadzany po obu stronach rury wlotowej B przed każdym suwakiem wlotowym Corlissa, następnie przepływa wraz z parą przez narząd wpustowy i po smarowaniu tłoka i oddaniu pracy przez ten ostatni, zostaje odprowadzony przez suwak wylotowy Corlissa.
Oprócz wprowadzenia oleju w strumień pary przed suwakami wlotowymi Corlissa, olej doprowadza się również wprost do kurków wlotowych w środku ich lub u końców, gdzie obrzeża suwaków przylegają do gładzi suwakowej cylindra. te ostatnie miejsca wymagają dobrego smarowania, więc też doprowadzanie na końcach należy uznać za lepsze, niż doprowadzanie w środku.
W ten sam sposób, jak w suwakach Corrlisa, doprowadza się olej i do stawideł z suwakami tłokowymi, a mianowicie u obu końców E. W czasach ostatnich jednakże przy tych trzech rodzajach stawideł, zwłaszcza w maszynach na parę przegrzaną, olej doprowadza się bezpośrednio do cylindra, lub też stosuje się smarowanie pośrednie cylindrów, przez doprowadzenie oleju do głównego przewodu parowego, w celu rozpylenia oleju w strumieniu pary.
 |
Smarownica mechaniczna z rozpylaczem |
1 - Zbiornik, 2 - Tłok, 3 - Dysza, 4 - Woda, 5- Zawór kulkowy wsteczny, 6 - Rurka doprowadzająca olej, 7 - Zawór sprężynowy, 8 - Rozpylacz, 9 - Wręby w rozpylaczu, 10 - Przewód parowy, 11 - Dośrubek, 13 - Nakrętka
W maszynach o stawidle zaworowym stosuję się często doprowadzanie oleju do komory zaworowej. Ten sposób doprowadzany jest na rysunku 21. Tak zwany rozpylacz oleju A znajduje się w strumieniu pary i para porywa ze sobą drobno rozpylony olej, który razem z nią przedostaje się do cylindra. Smarowanie poruszającego się pionowo trzona zaworu odbywa się za pomocą oleju, znajdującego się w parze, a dodatkowo z zewnątrz. Aby na skutek tworzenia się osadu przez zasychanie, lub spiekanie gęstego oleju cylindrowego zawory nie pozostawiały niedomknięte, należy codziennie smarować trzony z zewnątrz olejem maszynowym, za pomocą ręcznej oliwiarki przed rozruchem i po wstrzymaniu ruchu.
Bezpośrednie doprowadzanie olejów do cylindrów
Takie doprowadzanie olejów do obecnie bywa często stosowane : Olej doprowadzany jest w środku cylindra, lub w paru miejscach na obwodzie. Jeden z punktów doprowadzanie leży wówczas u wierzchołka cylindra. inne leżą o jedną trzecią obwodu cylindra niżej. W czasie ruchu okazuje się często, że doprowadzanie oleju w środku, u wierzchołka cylindra, wystarcza przy stosowaniu odpowiedniego oleju, tak że pozostałe miejsca doprowadzania oleju mogą być nie wyzyskane. Doprowadzenie oleju w dolnej połowie cylindra okazało się celowe tylko w specjalnych wypadkach.
Przy tych sposobach doprowadzania olej zostaje doprowadzony stopniowo przez tłok wzdłuż ścianek cylindra. Bezpośrednie doprowadzanie oleju wymaga zwykle większej jego ilości do smarowania cylindra, niż doprowadzanie oleju w strumieniu pary głównego przewodu parowego.
Pośrednie doprowadzanie oleju przez rozpylanie go w strumieniu pary głównego przewodu parowego.
Przy smarowaniu pośrednim olej, zamiast być doprowadzany bezpośrednio do różnych części, zostaje wprowadzony do przewodu parowego przed, a czasem po głównym zaworze przepustowym maszyny. W tym ostatnim wypadku olej zostaje jednocześnie doprowadzony również do trzonu zaworu, co ułatwia ruch zaworu, chociaż w ten sposób łatwiej powstają zakłócenia ruchu. Przez wprowadzenie oleju do strumienia pary zostaje on rozpylony, porwany przez parę i rozpostarty w postaci delikatnej warstewki na wszystkich częściach wewnętrznych.
Jeżeli przy tym para zostaje użyta do ogrzewania cylindrów i ich pokryw, zanim dopływa do cylindra ( co dzisiaj w maszynach parowych zdarza się dosyć rzadko ), to te komory grzejne działają, jako odoliwiacze. W tym wypadku lepiej jest doprowadzać olej cylindrowy tuż przed narządami stawidłowymi. Rozpylacz oleju 8 składa się z : prostki, wbudowanej w główny przewód parowy i zaopatrzonej w zawór wsteczny, albo lepiej zamknięcie olejem, a żeby zapobiec dopływowi pary do rurki, doprowadzającej olej. Para, przepływająca z dużą prędkością przez rurkę, wydmuchuje wtłoczony olej przez wręby 9, znajdujące się w łyżkowatym końcu rury, w który to sposób osiąga się rozpylanie.
Porwana przez parę mgła olejowa pokrywa wszystkie części wewnętrzne cieniutką warstewką oleju, tak , że zawory, tłok i drążki suwakowe oraz narządy rozrządcze są smarowane równomiernie i równocześnie bardzo oszczędnie. W maszynach o krótkim obiegu pary działanie to rozpościera się na całą maszynę, tylko w maszynach sprzężonych lub wielocylindrowych, w których pomiędzy poszczególnymi cylindrami, znajdują się większe przelotnie, te ostatnie mogą działać jako odoliwiacze.
Należy tutaj cylindry średnioprężne i niskoprężne smarować oddzielnie, mianowicie w ten sposób, że w przewód parowy między przelotnią a cylindrem wybuduje się się dalsze rozpylacze. W zależności od położenia rury, doprowadzającą parę świeżą, należy dobrać odpowiednie rurki rozpylacza. przy w budowie rozpylaczy dla oleju należy uważać, aby znajdowały się one w dostatecznej odległości od wlotu pary do cylindra; dla pary nasyconej nie poniżej jednego metra, dla pary przegrzanej mniej więcej jeden metr od narządu sterującego. W maszynach pewnych ustrojów i przy pracy parą wysoko przegrzaną ( ponad 400 stopni C ) rozpylacz umieszcza się bezpośrednio przed wlotem pary. Ażeby zapobiec strącaniu mgły olejowej, przewód rurowy od rozpylacza winien być możliwie prostoliniowy.
Zawory i kolanka działają jako chwytacze oleju, w których spieka się on i tworzy osad. Trudności powstają rzadko np. gdy szybkość pary jest zbyt mała lub gdy maszyna jest bardzo obciążona. Przy smarowaniu rozpryskowym można, najczęściej przy parze nasyconej, zrezygnować z zewnętrznego osobnego smarowania drąga tłokowego, ponieważ ten ostatni przez stykanie się z parą naoliwioną jest dostatecznie smarowany. Widać to po błyszczącym - olejowatym, matowo - gładkim wyglądzie powierzchni drąga.
Wymagania, stawiane smarowaniu najważniejszych części
W maszynach parowych, z wyjątkiem drągów tłokowych i suwakowych oraz trzonów zaworów, żadne inne części wewnętrzne, nie są widoczne tak, że warunki w jakich odbywa się smarowanie, nie mogą być obserwowane z zewnątrz. dlatego właściwe smarowanie części stawidłowych i cylindra stwarza znacznie więcej trudności, niż smarowanie części zewnętrznych. Smarowanie cylindrów maszyn parowych zależy w głównie od rodzaju stawidła, ciśnienia i temperatury pary, ilości obrotów, skoku i obciążenia.
Tłoki i cylindry
W maszynach stojących nacisk tłoka na ścianki jest mniejszy, dlatego wymagana jest mniejsza ilość oleju do smarowania cylindra, jak w maszynach leżących. W maszynach leżących, oprócz nacisku pierścieni tłokowych na ściankę cylindra, wchodzi w grę jeszcze działanie ciężaru tłoka i drąga tłokowego na dolną połowę cylindra. Dlatego większe maszyny leżące otrzymują zawsze, oprócz prowadzenia drąga tłokowego po stronie ku korbowej, jeszcze prowadzenie tylne, po stronie od korbowej. W ten sposób całkowity ciężar tłoka zostaje przenoszony z jednej strony na krzyżulec, z drugiej strony na wodzik. Warstwa smaru znajduje się pod działaniem temperatury pary i może być zniszczona przez nadmierny nacisk, tak że w wyniku mamy zwiększone tarcie, nadmierne zużycie i wcieranie się tłoka.
Pierścienie tłokowe mają zapobiec przepływowi pary z tej strony tłoka, która znajduje się pod wysokim ciśnieniem, na stronę znajdującą się pod niższym ciśnieniem. Dobry olej cylindrowy wspiera to uszczelniające działanie. Specjalną uwagę należy zwrócić na dobre zaokrąglenie krawędzi pierścieni tłokowych, gdyż ostre krawędzie zeskrobują warstewkę smaru ze ściany cylindra. Pierścienie tłokowe sporządzone są z metalu miękkiego, niż ścianki cylindra, należy bowiem przekładać ścieranie się pierścieni tłokowych nad ścieranie się ścianki cylindra, gdyż pierścienie tłokowe mogą być łatwiej zastąpione. Przy otwieraniu cylindra ścianka tego ostatniego winna posiadać matowy, olejowy wygląd.
Skoro po wytarciu ścianek występuje matowo - gładka powierzchnia, to smarowanie jest właściwe; odwrotnie - jeżeli powierzchnia ta jest lśniąco-metaliczna. Jeżeli do ścianki cylindra przyciśniemy kartkę papieru, to dowodem dobrego smarowania będzie, gdy na papierze widoczne będą ślady oleju.
Złe smarowanie cylindra, nie zawsze występuje w jaskrawej formie terkotania i wcieranie się tłoka. Pierwsze stadium złego smarowania poznajemy po występowaniu czystej, metalicznie błyszczącej powierzchni na ściance cylindra. Złe smarowanie cylindra może mieć różne przyczyny, z których główne są następujące: obrany został olej niewłaściwy, albo używa się oleju złej jakości, albo też ilość doprowadzonego oleju jest niedostateczna, lub nie zawsze równomierna.
Specjalny wpływ wywiera na smarowanie cylindrów para zanieczyszczona. W przeciwieństwie do smarowania łożysk, gdzie kontrola jest łatwo możliwa przez pomiar temperatury, lub w sposób podobny, przebieg smarowania cylindrów maszyn parowych, nie da się stwierdzić za pomocą przyrządów podobnych. Co do przypuszczalnego stanu smarowania, to można się w nim zorientować przez wysłuchiwanie szmerów w cylindrze w czasie biegu maszyny i przez pobranie próbek smarowania przez kurki indykatora. Wyciąganie wniosków za pomocą obu metod wymaga pewnej wprawy. Wysłuchiwanie szmerów w maszynie jest ogólnie stosowane, natomiast pobierania i ocena próbek smarowania nie wszędzie są stosowane dostatecznie.
Próbka smarowania zostaje pobrana w sposób następujący: kawałek szorstkiego papieru rysunkowego o wielkości około 15 x 15 cm zostaje umocowany na desce. Z otwartego kurka indykatora wypuszcza się parę w czasie 20 podwójnych skoków, po czym w odległości 10 cm od kurka umieszcza się deskę z przymocowanym papierem rysunkowym prostopadle do wypływającej pary i wystawia się papier na czterokrotny wydmuch pary z kurka indykatora. Należy to wykonać równocześnie dla obu stron cylindra.
Lepiej jest, skoro zamiast deski używa się przyrządu, który na przykład zostaje przyśrubowany do kurka indykatora i składa się zasadniczo z ramy w odległości 10 cm od wylotu kurka indykatora, w którą może być wstawiona płytka, przytrzymująca papier. Rzeczą najważniejszą przy pobieraniu próbek smarowania jest należyte wydmuchanie całkowicie otwartych kurków indykatora i wystawienie papieru przy każdej z porównanych próbek na zawsze jednakową ilość wydmuchiwanej pary.
Przy dobrym smarowaniu ślad smarowania daje charakterystyczną plamę kolistą o połysku od brunatnego do żółtego, która przy swoim brzegom staje się coraz jaśniejsza i słabsza. W razie w obecności w cylindrze osadów, niezależnie od tego, czy pochodzą one z oleju, czy powstały one przez zanieczyszczenia, próbka smarowania się tym oznacza, iż widnieje na niej czarna plama, usiana ziarnistymi albo błyszczącymi metalicznie, drobnymi punktami.
W kierunku brzegów tworzą się naokoło kolistego jądra czarne obłoczkowate osady. Pod mikroskopem lub dobrym szkłem powiększającym, możne dobrze rozróżnić starte cząsteczki z cylindra i pierścieni tłokowych. Zbyt obfite smarowanie uwidacznia próbka o połysku tłustym, na której olej osadza się promieniowato. Przy nie dostatecznym doprowadzeniu oleju następuje ścieranie się części i olej zabarwia się na ciemno.
Granice rozpoznaje się po bardzo słabej, delikatnej jak chuchnięcie, jasno żółtej próbce smarowania, na której słabo daje się rozróżnić tylko jądro próbki. dobre rozprowadzenie oleju poznaje się po możliwe dużej i jednostajnie próbce smarowania, podczas gdy złe rozprowadzanie oleju poznajemy, po próbce złożonej z części oddzielnych.
Skoro stosuje się olej niewłaściwy, to wydzielają się osady, które jak przedtem oznaczono, poznaje się po czarnych próbkach smarowania. Może nastąpić jednakże również parowanie i rozkład oleju, co poznaje się nie tylko po ciemnym zabarwieniu, lecz jeszcze i po stalowym - szarym osadzie na brzegach jądra próbki.
Dla stałej kontroli smarowania wewnętrznego maszyn parowych konieczne jest pobieranie próbek smarowania w regularnych odstępach czasu i w dokładnie w ten sam sposób. Ważne jest aby zawsze była zachowana ta sama odległość od kurka indykatora do papieru, na którym powstaje próbka i aby używano zawsze jednego gatunku papieru.
Suwaki płaskie
Ruch przymusowy stawidła z suwakiem płaskim teoretycznie zezwala na stosowanie dowolnych szybkości. Jednakże ze względu na złe wyrównanie mas ( duże masy poruszające się wzdłuż i wszerz ), nie nadaje się ten rodzaj stawidła do stosowania tak dużych prędkości, jak w stawidłach z suwakiem tłokowym. W suwaku płaskim mamy duże powierzchnie cierne, których smarowanie jednostajne przedstawia duże trudności, wobec czego w wielu wypadkach nacięte są specjalne wpustki do oleju, które umożliwiają lepsze smarowanie.
Obszar zastosowania suwaka płaskiego jest ograniczony ze względu na stosunkowo duże płaszczyzny cierne. Bywa on używany tylko przy umiarkowanych prężnościach pary i temperaturach. Utrzymanie całkowitej powłoki olejowej pomiędzy gładzią suwakową a licem suwaka jest o wiele trudniejsze, niż na przykład pomiędzy wałem, a łożyskiem. Przy smarowaniu wału w łożysku olej dzięki swoim właściwościom kapilarnym zostaje wciągnięty w klinowany luz pomiędzy łożyskiem a wałem, od miejsc niskiego nacisku ku punktom najwyższego nacisku, a więc do miejsca podparcia.
Ponieważ smarowanie powierzchni płaskich odbywa się w warunkach niekorzystnych w porównaniu do smarowania powierzchni okrągłych, ze względu na niemożliwość wytworzenia klinowatego luzu, staramy się w suwakach dużych trudność tę usunąć w ten sposób, iż budujemy suwaki odciążone. Bardzo wysokie ciśnienie pary uniemożliwiałoby, zwłaszcza przy zastosowaniu zwykłych, nieodciążonych suwaków płaskich, wytworzenie się dostatecznej warstewki oleju, na skutek czego płaszczyzny ślizgałyby się po sobie z dużym tarciem i przy znacznym ścieraniu się powierzchni.
Bardzo wysoka temperatura wywoływałaby nieregularne rozszerzanie się pod wpływem ciepła i tak zwane " paczenie się " suwaka i gładzi suwakowej, zaś w wyniku tego nieszczelność. to znów znacznie zwiększa zużycie się oleju gdyż jednocześnie ze zbędnym wypustem pary, ta ostatnia porywa ze sobą i olej. Powierzchnie nie całkiem już płaskie mocno się ścierają, tak, że nie może się już wytworzyć ciągła warstewka oleju pomiędzy ślizgającymi się po sobie powierzchniami.
Po otworzeniu skrzynki suwakowej można stwierdzić nadmierne tarcie po zagrzanych, pokrytych bruzdami powierzchniach. Ważne jest, żeby żeliwo, z którego sporządzona jest gładź suwakowa, było cokolwiek twardsze, niż żeliwo suwaka, tak aby suwak ścierał się więcej, niż gładź suwakowa, gdyż łatwiej jest zamienić lub na nowo dotrzeć suwak, niż gładź suwakową, która stanowi całość z cylindrem. Czasami wstawia się również do skrzynki suwakowej specjalną płytkę, która się w razie silniejszego zużycia wymienia.
Czasami o tarciu suchym suwaka płaskiego ostrzega nas terkotanie przy równoczesnym drganiu drążka mimośrodowego na skutek nadmiernego tarcia. Przy smarowaniu należytym suwak pracuje bez najmniejszego szmeru, a oznaką tego jest, iż zarówno gładź, jak i lico suwaka przy oglądaniu przedstawiają matową, gładką powierzchnie. Całkowicie ogólnie matowy, nie zaś suchy błyszczący wygląd powierzchni jest oznaką dobrego smarowania.
Często smarowanie pośrednie usuwało szmery i inne trudności, powstające przy użyciu suwaków płaskich, skoro metoda smarowania bezpośredniego dawała wyniki niedostateczne.
Suwak tłokowy
W przeciwieństwie do zwykłego suwaka płaskiego, suwak tłokowy jest ciałem cylindrycznym i jest całkowicie odciążony. Rozszerzanie się suwaka tłokowego pod wpływem podwyższonej temperatury pary odbywa się ze względu na jego symetryczną budowę równomiernie, we wszystkich kierunkach, dzięki czemu zapobiega się jednostronnemu zacinaniu. W ten sposób temperatura i prężność pary posiadają na pracę suwaka tłokowego, zwłaszcza zaopatrzonego w pierścienie w pierścieniu uszczelniające, znacznie mniejszy wpływ, niż na pracę suwaka płaskiego.
Smarowanie suwaka tłokowego jest wobec tego połączone z mniejszymi trudnościami. Należy baczyć, aby olej został rozprowadzony możliwie równomiernie na powierzchniach ślizgowych, i tutaj smarowanie za pomocą rozpylaczy okazało się najlepsze. Zewnętrzne oznaki dobrego lub złego smarowania są te same, jak w suwaku płaskim.
Suwaki lub kurki Corliss'a
Podczas gdy suwak płaski wykonuje ruch posuwisty ( przód, tył ) po powierzchni płaskiej, to suwak Corlissa wykona ruch wahadłowy po powierzchni cylindrycznej. Strony ujemne, jakie pociągają za sobą bardzo wysoka temperatura i bardzo wysokie ciśnienie pary, przy zastosowaniu suwaków płaskich, a takie same również i przy zastosowaniu suwaków Corliss'a. Przy zastosowaniu dzisiaj wysokich temperatur pary i wysokich prężnościach użycie tego stawidła pociąga za sobą liczne trudności, gdyż tak samo, jak suwak płaski, suwak Corlissa posiada skłonność do zatarcia się o gładź suwakową.
Nadmierne tarcie, spowodowane złym smarowaniem, daje się rozpoznać po szmerach i drganiu części ruchomych. Przy złym smarowaniu, na wyjętym kurku Corrlisa widoczne są te same oznaki, jakie zostały omówione przedtem dla suwaków płaskich. I tutaj bezpośrednie działanie oleju do suwaków Corrlisa, często prowadzi do zwiększonego zużycia oleju lub niedostatecznego smarowania i na odwrót, rozpylanie oleju przez parę jest znacznie korzystniejsze i przy zastosowaniu odpowiedniego oleju daje, gładki i lekki bieg.
Stawidło zaworowe
Dawniej zawory posiadały siodła stożkowe, gdyż myślano, iż w ten sposób uzyska się większą szczelność; obecnie robi się siodła płaskie, gdyż i w ten sposób można osiągnąć całkowicie szczelne domknięcie, a z drugiej strony zmniejsza się nie bezpieczeństwo niezawierania się ( chwytania się ) zaworów, co jest znacznie większe przy siodłach stożkowych, co jest znacznie większe przy siodłach stożkowych. Zawór siedzi w swoim siodle i przy otwieraniu unosi się z siodła, co odbywa się bez tarcia, tak że zbędne jest smarowanie siodła zaworu. Natomiast trzon zaworu wykonywa krótki ruch w swojej prowadnicy w zależności od skoku zaworu, wobec tego tylko trzon zaworu wymaga pewnego smarowania.
W tym celu używa się nie tylko oleju cylindrowego, ale od czasu do czasu do smarowania odręcznego również i oleju maszynowego. Właśnie ten lżejszy olej maszynowy posiada własność rozpuszczania osadów na zaworach i zapobiega przez to chwytaniu się zaworów. Powierzchnia wrzeciona zwykle posiada wytyczona ilość rowków, które działając jako uszczelnienie grzebieniaste, jednocześnie rozprowadzają olej. Ponieważ ciężki olej cylindrowy z rowków tych nie wycieka więcej, więc stopniowo, pod wpływem gorąca, zanieczyszczeń pary i ewentualnie powietrza, spieka się, powstające w ten sposób osady wpływają stale hamująco na łatwą ruchliwość trzona. Zgęszczający się olej zostaje rozpuszczony przez lekki olej maszynowy, co zapobiega tworzeniu się osadu. Również przy zastosowaniu tego stawidła metoda rozpryskowa daje dobre wyniki.
Dławice
Dławice na drągach tłokowych i narządach stawidłowych mają na celu zapobieżeniu uchodzenia pary, oraz dostępowi powietrza do cylindra, niskoprężnego w maszynach ze skraplaczem. Dobre i skuteczne smarowanie dławic jest bezwzględnie konieczne, z jednej strony, aby ograniczyć w miarę możliwości tarcie w dłąwicy, z drugiej strony, aby zapewnić zupełną szczelność. Dobrze rozprowadzona warstewka oleju na drągu tłokowym i w dławicy podobnie jak między pierścieniami tłokowymi, a ścianką cylindra, jest najlepszym środkiem uszczelniającym, nawet przy pracy parą wysokoprężną przegrzaną.
Smarowanie dławic może się odbywać bądź przez smarowanie kroplowe drąga tłokowego, bądź też przez bezpośrednie doprowadzanie oleju cylindrowego pod ciśnieniem do szczeliwa metalowego. Sposób ten jest stosowany zwłaszcza w maszynach na parę przegrzaną. Smaruje się przy tym najczęściej tylko dławice wysokoprężne i należy doprowadzać olej w miarę możliwości jak najbliżej końca wewnętrznego dławicy, gdyż przez ciśnienie pary zostanie on samoczynnie wyciśnięty na zewnątrz. W cylindrach niskoprężnych w wielu wypadkach smarowanie osobne dławic jest zbędne, zwłaszcza jeżeli smaruje się przez wprowadzenie oleju w strumień pary. Skoro jednak przelotnia pomiędzy cylindrem wysokoprężnym, a niskoprężnym działa również jako odoliwiacz, to wówczas bezpośrednie smarowanie dławicy cylindra niskoprężnego jest mimo to celowe.
Ze względu na próżnię w cylindrze niskoprężnym olej przy smarowaniu dławicy zostaje raczej wtłaczany ku wnętrzu, nie zaś wyciskany na zewnątrz, i dlatego w tym wypadku olej należy doprowadzać bliżej zewnętrznego końca dławicy. W wielkich maszynach stosuje się zarówno smarowanie kroplowe, jak i smarowanie pod ciśnieniem, osobno lub jednocześnie. Przy osobnym smarowaniu szczeliwa zwłaszcza przy pracy wysoko przegrzaną parą należy baczyć, aby zapewnione było oszczędne, równomierne doprowadzanie oleju, gdyż w przeciwnym razie olej osadza się między pierścieniami, spieka się, przy czym gromadzi się tam osad.
Wybór oleju cylindrowego
Zasady smarowania
Dawniej, w początkach rozwoju techniki silników parowych, sprawie smarowania poświęcono tylko niewielką uwagę i smarowanie maszyny odbywało się za pomocą pierwszego lepszego oleju, przy czym nie zastanawiano się głębiej, ani nad przebiegiem smarowania, ani nad niezbędnymi własnościami smarów. Prace wykonane w technice i nauce na przestrzeni dziesiątek lat, posunęły naprzód wiedzę o technice smarowania. Do najszerszych kół przeniknęła już świadomość, że dla każdego wypadku smarowania należy dodać smar najodpowiedniejszy w danych warunkach dla uzyskania najskuteczniejszego smarowania.
Jednakże raz jeszcze przypominamy w tym miejscu, że tylko właściwy olej, na właściwym miejscu, może całkowicie rozwiązać sprawę, dwu ślizgających się po sobie powierzchni. Nie wystarcza aby olej był doprowadzany w jakimkolwiek punkcie powierzchni, które mają by smarowane, ale należy starać się o to, aby olej został rozprowadzony po całej powierzchni. Niezbędne jest przede wszystkim, wytworzenie się nie przerwanej, równomiernej powłoki smarnej, która zapobiega tarciu suchemu i półsuchemu. Tej wytycznej wytworzenia się zupełnej powłoki olejowej przeciwstawiają się własności cząsteczkowe olejów smarnych, jak np. ciekłość i napięcie powierzchniowe. Smarowanie dwu ślizgających się po sobie powierzchni jest możliwe bez zastosowania bardzo złożonych przyrządów pomocniczych tylko za pomocą płynów, które posiadają własność zwilżania.
Płyny niezwilżające jak na przykład rtęć, mogą być wtłoczone między dwie ślizgające się powierzchnie tylko pod bardzo wysokim ciśnieniem i przy najmniejszym odciążeniu lub niesymetrii istnieje niebezpieczeństwo, że płyn niezwilżający wyślizgnie się z pomiędzy powierzchni, które mają być smarowane. W inny sposób zachowują się płyny, posiadające własność zwilżania, którą chodź w stopniu różnym, posiadają wszystkie smary; olej smarny zostaje wciągnięty dzięki włoskowatości do miejsc najwęższych miedzy dwiema płaszczyznami i tworzy jednolita powłokę olejową, która jest niezbędna do całkowitego smarowania.
Jak zostało dowiedzione przez inne zjawiska fizyczne, te siły włoskowatości przybierają bardzo wielkie, wprost niespodziewane rozmiary i wycisnąć smar z pomiędzy dwóch powierzchni można tylko za pomocą bardzo wysokiego, jednostronnego nacisku. Poniżej omówione będzie tylko smarowanie cylindrów.
Warunki podstawowe i wymagania
Warunki smarowania wewnętrznego maszyny parowej są następujące :
1. Utworzenie powłoki olejowej pomiędzy ślizgającymi się powierzchniami, tak aby tarcie metaliczne powierzchni smarowanych zastąpić przez wewnętrzne tarcie cieczy.
2. Powstanie warstwy uszczelniającej, która doszczelnia narządy sterujące, tłok i dławice. Dzięki zastosowaniu wysokowartościowego, dobranego należycie oleju, na wszystkich wewnętrznych powierzchniach ciernych utrzymana zostaje nieprzerwana warstewka smaru. Straty siły, spowodowane nieszczelnością powierzchni ruchomych i tarciem ciekłym oleju są ograniczone do minimum. Utrzymanie tej powłoki olejowej odbywa się przy najmniejszym zużyciu smaru.
Przy doborze właściwego oleju cylindrowego dla maszyn parowych należy uwzględnić następujące punkty zasadnicze:
1. Olej powinien oddać się całkowicie rozpylaniu, posiadać w stopniu wysokim zdolność rozpościerania się oraz pokrywania warstewką jednostajną wszystkich części organów rozrządczych i cylindra. To jest zależne nie tylko od gatunku i jakości oleju, lecz również od własności, chyżości i ilości pary, dopływającej do cylindra.
2. Olej musi posiadać zdolność możliwie długiego utrzymywania wystarczającej, niezmiennej powłoki smarnej. Skutkiem tego jest oszczędne zużycie smaru, a przede wszystkim dobra konserwacja części ciernych, a więc najmniejsze ścieranie się i mała ilość napraw. Czynnikiem ważnym jest tutaj lepkość i jakość oleju oraz wysokość temperatury i działanie płóczne, wywierane przez parę na warstewkę smarną.
3. Olej powinien być wolny od części składowych, które mogą być przyczyną rozkładu lub rozkładowi temu sprzyjać. Olej nie powinien zawierać w sobie twardego asfaltu, popiołu, kwasów i zasad. Jednakże wyniki analizy chemiczno-fizycznej, głównie zaś punkt zapłonu i ciekłość ( wiskoza ) oleju, nie określają bynajmniej wartości smaru. Zastosowanie oleju winno być uwzględnione już przy wyborze surowca i jego przeróbce, a te ostatnie znowu nie mogą być stwierdzone z wyników analizy.
Maszyny parowe na parę wysoko przegrzaną wymagają olejów ciężkich o bardzo dobrej czepności w tym celu, aby warstewka oleju pomiędzy częściami ruchomymi została utrzymana. Odwrotnie, do smarowania maszyn parowych o niskiej prężności pary i niskich temperaturach, przy niewielkim obciążeniu i zużyciu pary używa się stosunkowo lekkiego oleju o dobrej czepności, aby zapewnić dostateczne rozpylanie i rozprowadzanie.
Użycie zbyt ciężkiego oleju przy niewielkiej prężności i niskiej temperaturze pary, może przynieść w wyniku nieprawidłowe rozprowadzenie i duże zużycie oleju, a może sprzyjać tworzeniu się osadów, w cylindrze i na pierścieniach tłokowych, skoro para dolotowa zawiera nieczystości. Przy użyciu zbyt lekkiego oleju rozprowadzanie tego ostatniego jest łatwe, ale nie może się on oprzeć naciskowi powierzchni ślizgających się po sobie, powłoka olejowa zostanie przerwana, wreszcie zupełnie wyciśnięta, a wynikiem jest tarcie mechaniczne, nadmierne zużycie i wielkie straty pary.
Zbyt obfite doprowadzenie oleju nie polepsza smarowania. Wzmaga się jedynie powstawanie osadu, zwłaszcza skoro para zawiera zanieczyszczenia. To dotyczy zwłaszcza pary przegrzanej. Właściwa ilość wysokowartościowego oleju zapewnia zawsze właściwe smarowanie. Przy niedostatecznym dopływie smaru nie można stale utrzymać nieprzerwanej powłoki smarnej, działanie uszczelniające oleju jest niewystarczające, a w wyniku mamy straty pary, niedostateczne smarowanie i objawy nadmiernego zużycia.
Warunki pracy
Dobór, właściwego oleju do smarowania cylindrów zależy w zasadzie od następujących warunków :
- Wielkości maszyny
- Szybkości tłoka
- Obciążenia
- Prężności pary
- Rodzaju pary
Wielkość maszyny
Ilość pary dopływająca do cylindra w czasie jednego skoku, zależna jest od wielkości maszyny. Od wielkości napełnienia zależy okres czasu, w przeciągu którego odbywa się wlot pary. Ilość pary i czas trwania wlotu są miarodajne dla rozpylania i rozprowadzenia oleju. Promieniowanie ciepła również zależy od wielkości maszyny, mianowicie jest ono w małych maszynach znacznie większe, niż w dużych. Na skutek tego w maszynach dużych ciężko płynny olej daje się łatwiej doprowadzać i rozprowadzać, a także utrzymuje łatwiej stosunkowo grubszą powłokę olejową, podczas gdy dla maszyn mniejszych należy polecić olej łatwo płynny.
Szybkość tłoka
Średnią prędkość tłoka w metrach na sekundę, obliczamy mnożąc suw tłoka przez ilość skoków tłoka na sekundę. Ilość skoków tłoka na minutę wskazuje, ile razy para dopływa do cylindra. Czas trwania skoku określa trwanie wpływu temperatury na rozpylanie. Maszyny wielkie pracują zwykle jako wolnobieżne, tzn. z małą ilością obrotów. W maszynach wolnobieżnych odziaływanie cieplne pary na rozpylanie i zdolność rozpościerania się oleju cylindrowego jest bardziej długotrwałe i sprzyja zastosowaniu oleju ciężko płynnego. Na odwrót działanie cieplne pary w maszynach szybko bieżnych ( zwykle małe maszyny ) na rozpylanie i zdolność rozpościerania się oleju cylindrowego jest krótsze i odpowiedniejsze jest stosowanie oleju łatwiej płynnego, dającego się szybciej rozprowadzać.
Obciążanie
Gdy maszyna pracuje z mocą nominalną, to para zostaje wykorzystana, to para zostaje wykorzystana najekonomiczniej. Maszyny parowe są jednak silnikami elastycznymi, mogącymi pracować przy obciążeniu wyższym lub niższym, niż moc nominalna, przy czym jednak sprawność nie jest taka sama, jak przy mocy nominalnej. Smaru cylindrowego, dobranego, do warunków normalnych ruchu i obciążenia 765 i 100 % mocy nominalnej, nie można użyć jednakowo korzystnie w maszynie, która pracuje stale przy małym obciążeniu, to znaczy poniżej 75 %.
Skoro maszyna jest przeciążona, osiąga się zupełne rozpylenie i rozprowadzenie oleju na wskutek większej ilości pary dolotowej i dłuższego wlotu. Poza tym skraplanie pary wewnątrz cylindra nie ma miejsca ze względu na większą ilość cieplika, doprowadzonego co skok. W tych warunkach może wytworzyć się bardzo dobra powłoka olejowa, tzn. doprowadzona ilość oleju daje się doskonale rozprowadzić i nie ma obawy, że zostanie wypłukana przez parę skraplającą się wewnątrz cylindra, jak to łatwo może się zdarzyć przy niskim obciążeniu. Olej cylindrowy, polecany przy obciążeniu nominalnym, może być używany i dla obciążeń powyżej mocy nominalnej, przy oszczędnym nastawieniu zużycia oleju.
Gdy maszyna parowa pracuje z mniejszym obciążeniem, to w czasie skoku dopływa stosunkowa mniejsza ilość pary, co prowadzi do skraplania się pary w cylindrze a krótszy wlot sprawia, że olej cylindrowy, nie zostaje tak skutecznie porwany przez parę i rozprowadzą, jak wtedy gdy maszyna oddaje moc nominalną. W tych warunkach odpowiedniejszy będzie olej łatwo płynny, dający się prędzej rozprowadzać. Poza tym obecność skraplającej się pary w cylindrze prowadzi łatwo do uszkodzenia powłoki olejowej. Aby temu zapobiec, olej cylindrowy powinien być natłuszczony.
Własności olejów roślinnych lub zwierzęcych, używanych do natłuszczenia, zwiększają zdolność olejów mineralnych zdolności czepiania się powierzchni ślizgowych, przeciwstawiając się w ten sposób działaniu pary skroplonej. W maszynach pracujących przy małym obciążeniu, należy więc używać oleju, różniącego się od oleju używanego przy pełnym obciążeniu. Łatwo płynny, natłuszczony olej cylindrowy ( olej złożony ), używany oszczędnie będzie najwłaściwszym smarem.
Prężność pary
Siła i trwanie nacisku pary na części smarowane ( to znaczy narządy sterujące, pierścienie tłokowe, ścianki cylindrów i szczeliwo w dławicach drąga tłokowego ) wywierają wpływ na utrzymanie warstewki smarnej. Prężności pary odpowiadają pewne temperatury, które mogą być podniesione przez przegrzanie, zaś stale są obniżane przez promieniowanie ciepła.
Wysoka prężność pary wraz z odpowiadającą jej temperaturą pary nasyconej lub temper aurą pary przegrzanej wymaga zastosowania oleju cylindrowego trudno płynnego. Średnie prężności pary i odpowiadająca im temperatura pary nasyconej wymagają stosowania oleju cylindrowego o średniej płynności. Niskie prężności pary i odpowiednio niska temperatura sprzyjają zastosowaniu lekko płynnego, natłuszczonego oleju.
Własności pary
Para może zawierać prężność wysoką lub niską; może być mokra, sucha, nasycona lub przegrzana. Parę mokrą nazywamy parę, zawierającą więcej, niż 3% wilgoci, mierząc bezpośrednio przed maszyną. Skoro para w drodze do silnika może pokryć straty ciepła, wywołane przez promieniowanie, a odpowiadające zawartości wilgoci do 3%, to parę taką nazywamy w praktyce parą suchą nasyconą. Jeżeli do pary nasyconej doprowadzamy ciepło przy stałym ciśnieniu ( przegrzewamy ją ), to otrzymujemy parę przegrzaną.
Prężność pary, stosowane obecnie w silnikach parowych, nie są tak wysokie, aby odpowiadające im temperatury suchej pary nasyconej wynosiły więcej, niż 315 stopni C, mierząc tuż przed cylindrem. Naprz. prężności 30 at. abs. odpowiada temperatura pary 232.77 stopni C. Dlatego można powiedzieć na ogół, że jeżeli temperatura pary wynosi powyżej 315 stopni C. mierząc tuż przed cylindrem, to jest to para przegrzana, nie zaś para nasycona o odpowiednio wysokiej prężności.
Jak wykazała praktyka, temperatura ta jest granicą, powyżej której stosuje się specjalnie ciężki, odpowiedni dla wysoko przegrzanej pary, olej cylindrowy, skoro obciążenie maszyny wynosi więcej, niż 75% - Dla suchej nasyconej lub przegrzanej pary do 315 stopni C. stosuje się olej cylindrowy średnio lub trudno płynny. Dla pary mokrej stosowany bywa średni, lekko płynny, dobrze natłuszczony olej cylindrowy. Miarodajne dla doboru oleju cylindrowego, który ma odpowiadać danym własnościom pary, jest natężenie cieplne i zdolność rozpościerania się oleju przy danych własnościach pary.
Oleje cylindrowe Gargoyle do smarowania maszyn parowych
Olej cylindrowy Gargoyle Extra Hecla jest odpowiedni dla maszyn o obciążeniu powyżej 75%, pracujących parą przegrzaną o temperaturze ponad 315 stopni C. mierzonej tuż przed cylindrem, szybko lub wolnobieżnych. W tych samych warunkach ruchu, jak wymienione przedtem, jednakże przy temperaturze pary, mierzonej tuż przed cylindrem nie wyżej, niż 315 stopni C. i prężności pary powyżej 7 at. nadc. należy stosować olej średnio ciężki. Większość maszyn parowych, pracuje w tych warunkach, a olej dla nich odpowiedni, to Gargoyle Cylinder 600 W.
Skoro zadaniem naszym jest dobrać olej odpowiedni dla maszyny dużej, pracującej parą suchą i przy obciążeniu ponad 75%, lub o maszyny na parę przegrzaną o dowolnej temperaturze pary i obciążeniu ponad 75% mocy nominalnej, to należy uwzględnić, że para w cylindrze nie posiada tej zdolności rozdzielczej i , że średnia ścianek jest niższa. W wypadkach takich najodpowiedniejszy jest olej cylindrowy średniociężki o wysokiej smarności, na przykład olej Gargoyle Valve Oil Navy.
Gargoyle Valve Oil Navy okazał się odpowiedni przy uwzględnianiu zachowania się pary w następujących warunkach ruchu. Dla małych maszyn wolnobieżnych, pary mokrej o każdej prężności, wysokiego obciążenia ponad 75% mocy nominalnej oraz dla maszyn dużych o dowolnej ilości obrotów i obciążeniu i pary mokrej ponad 7 atmosfer.
Jeżeli obciążenie małej maszyny parowej spada poniżej 75% jej mocy nominalnej to mimo temperatury pary do 315 stopni C, mierzonej tuż przed cylindrem, można osiągnąć smarowanie zupełne, tylko za pomocą oleju lekkiego. W tych wypadkach okazał się szczególnie odpowiedni Gargoyle Cylinder Oil Rarus. Ten sam olej w doskonały sposób nadaje się do warunków takich, jakich wymaga smarowanie cylindrów niskoprężnych dużych i średnich maszyn parowych.
Wbrew ogólnie rozpowszechnionemu mniemaniu, że tylko czysty olej mineralny posiada zupełną zdolność wydzielania się z pary odlotowej, doświadczenie wykazało, że wysoko wartościowe, należycie dobrane, odpowiednio natłuszczone oleje cylindrowe pod względem zdolności wydzielania się w niczym nie ustępują czystym olejom mineralnym. Doświadczenie wskazuje dalej, że zużycie olejów natłuszczonych zwykle jest znacznie niższe od zużycia czystych olejów mineralnych, przy czym niezbędną pewność ruchu nic na takiej zamianie nie traci.
W tym zawarta jest, obok lepszego działania smarnego, znaczna korzyść. Dzięki możliwości osiągnięcia mniejszego jednostokowego zużycia oleju, co się wyraża w mniejszym ogólnym zapotrzebowaniu oleju, co się wyraża w mniejszym ogólnym zapotrzebowaniu oleju, zmniejsza się również możliwość przeszkód w ruchu. Przeszkody takie mogą powstać w razie nienormalnych warunków ruchu, które czasem powstają tylko przejściowo, jak na przykład zanieczyszczenia pary, a stąd tworzenie się osadów w maszynie.
Jeżeli stosujemy olej zupełnie dobry, lecz nie nadający się do użytku oszczędnego, gdyż wtedy smarowanie jest niedostateczne, to czasem wywołuje to tworzeniem się osadów, zwykle zaś wzmaga się ich powstawanie przez zbyt obfity dopływ oleju, co sprawia, że przeszkody w ruchu są nieuniknione. Aby uzyskać smarowanie oszczędne, niezbędne jest zastosowanie smarownicy, dającej możliwość regulowania z całą pewnością ilości doprowadzonego oleju, jak np. smarownica Delvac'a.
Oleje cylindrowe Gargoyle dają się odzyskać z powrotem z pary odlotowej lub skroplin w wysokim stosunku procentowym, odpowiednim do danych warunków i tak w niezmienionym stanie , iż mogą być ponownie użyte do smarowaniach w tych samych miejscach. Jest to dalsza korzyść, związana z użyciem olejów cylindrowych Gargoyela, która w wyższym jeszcze stopniu zapewnia oszczędność w smarowaniu. Tylko w zupełnie specjalnych warunków ruchu należy wybierać nienatłuszczone oleje cylindrowe mineralne jak Gargoyle Cylinder Oil 600. W mineral, Gargoyle Cylinder Oil Rarus i.t.d zamiast natłuszczonych takich samych gatunków oleju cylindrowego. Należy przy tym zauważyć, że zgodnie z wywodami, o których mowa wyżej, zużycie oleju w porównaniu do zużycia olejów natłuszczonych okaże się z konieczności większe.
Usługi Fachowców dla dobierania właściwych smarów
W przykładach przytoczonych wyżej, poruszony został w sposób ogólny zakres zastosowania wymienionych olejów cylindrowych. Jednakże w wypadkach poszczególnych, zwłaszcza w wypadkach leżących na pograniczu, dobór właściwego oleju musi być pozostawiony po dokładnym zbadaniu warunków inżynierom fachowcom techniki smarowania.
Smarowanie mechanizmu ruchu
W maszynach dawniejszych stosowano do smarowania mechanizmu ruchu smarowanie kroplowe i pierścieniowe, w wypadkach uosobionych nawet knotowe. W ostatnim czasie stosuje się coraz więcej smarowania obiegowego. Rozróżniamy smarowanie obiegowe bez ciśnienia i smarowanie obiegowe pod ciśnieniem. W tym pierwszym olej zostaje doprowadzony za pośrednictwem zbiornika, z którego olej pod właściwym ciężarem rozchodzi się przez sieć rurek do miejsc smarowanych. Przed tymi ostatnimi wbudowane są zwykłe w przewody wzierniki do sprawdzania ilości doprowadzonego oleju. Olej, spływający z miejsc użycia odpływa do zbiornika, skąd zostaje zabierany przez pompkę znowu do zbiornika rozdzielczego.
Smarowanie obiegowe pod ciśnieniem różni się od poprzedniego zasadniczo tym, że olej doprowadzany jest pod ciśnieniem przez pompkę wprost do miejsc smarowanych. Poza tym obieg kołowy odbywa się w podobny sposób, jak w systemie obiegowym bez ciśnienia. Dla ciągłego ciśnienia oleju w system obiegowy wbudowane zostają filtry, co sprawia, że olej dłużej zostaje zatrzymany w stanie zdatnym do użytku.
W maszynach parowych, zwłaszcza w maszynach o całkowicie zamkniętym mechanizmie ruchu, istnieje obawa, że przez ciepło promieniujące lub przez ciepło oddawane przez drąg tłokowy, olej zostanie wystawiony na działanie wysokich temperatur, pewne oleje okazują skłonność do kopcenia. To jest potęgowane poprzez tworzenie się mgły olejowej powstającej przez rozpryskiwaniu oleju przez korbę. Mgła olejowa przechodzi w parę olejową przy zetknięciu z gorącym drągiem tłokowym i dławnicą.
Należy to wziąć pod uwagę przy doborze smaru, który musi się specjalnie do tego celu nadawać. Oleje nie odpowiednie, użyte w miejscu tym, mogą przez obłożenie skoksowanym smarem dławic doprowadzić do stopniowego zniszczenia tych ostatnich, a wreszcie wzmaga się niebezpieczeństwo zatkania przewodów, doprowadzających olej, przez powstający osad. Dalsza niezgodność, zagrażająca skutkiem tworzenia się pary olejowej, polega na możliwości zniszczenia izolacji elektrycznej prądnic, które często jak wiadomo, wbudowane są w koła zamachowe maszyn parowych.
Tworzenie się pary olejowej, zwłaszcza w stopniu silniejszym, jest uciążliwe dla obsługi maszyny. Smarowanie obiegowe należy uznać za najbardziej celowy system smarowania. Przy smarowaniu tym olej zostaje obficie doprowadzony do miejsc smarowanych, dzięki temu osiąga się nie tylko pewny, wystarczający dopływ smaru, ale również dobrze działanie chłodzące.
Smarowanie obiegowe wobec wielokrotnego użycia tego samego oleju do smarowania oraz wystawienia oleju w czasie jego obiegu na działanie ciepła i tlenu atmosferycznego jest połączone ze znacznym natężeniem oleju. Dlatego do użytku tego nadają się tylko wysokojakościowe, czyste oleje mineralne o wysokiej wartości smarnej i dużej trwałości. Olej nie powinien wykazywać ( przy nieuniknionym przypływie wody ) skłonności do tworzenia emulsji, ani też nie powinien w obecności zanieczyszczeń zmydlać się, gdyż w obu wypadkach efekt smarny natychmiast uległby poważnemu zmniejszeniu.
W system obiegowy włączane są często hydrauliczne urządzenia podporowe dla cylindrów oraz regulator olejowy. Spotyka się również regulatory poruszane parą odlotową lub przelotową, a sterowane przez serwomotor za pomocą oleju pod ciśnieniem. W maszynach z odbiorem pary regulatory takie mogą być nastawiane, w zależności od pożądanego przeciwciśnienia albo zapotrzebowania pary do celów grzejnych. Olej do tych regulatorów powinien posiadać dużą trwałość i czystość, a przy tym mieć taką płynność, aby opory przepływu przez przekroje regulatora nie były źródłem zbyt wielkich strat.
Woda lub inne zanieczyszczenia, które mogą się dostać do oleju w regulatorze, powinny być łatwo i szybko wydzielane, tak aby usterki w pracy regulatora z tego powodu były wykluczone.
Odzyskiwanie olejów
Oleje wysokowartościowe winny być w celu osiągnięcia przy ich zastosowaniu najlepszych rezultatów pod względem oszczędności, regenerowane w ten sposób, aby odzyskany olej starannie oczyszczony mógł być użyty ponownie do smarowania. Jak wzmiankowano przedtem olej wysokowartościowy, właściwie dobrany, nie traci w warunkach dobranych przez jednokrotne użycie swoich własności i może po należytym przygotowaniu i zmieszaniu z olejem świeżym, znowu być użyty do smarowania cylindrów silników parowych.
Z odoliwiacza pary mieszanina wody i oleju zostaje doprowadzona do osadnika. Olej jednakże, który się tu zbiera, przed zastosowaniem ponownym, powinien być jeszcze ogrzany ( niżej temperatury wrzenia wody ) przefiltrowany lub przepuszczony przez wirówkę. Filtrowanie ma na celu wydzielenie wody i zanieczyszczeń mechanicznych przez osadzanie się i przepływania przez ciała filtrujące ( odpadki wełny, ciała o dużej powierzchni itd. ) Ten sam skutek osiąga się przez działanie wirówki.
Zwykle używa się wirówek w formie tak zwanych filtrów odrzutowych (odśrodkowych ). Pracują one w ten sposób, że olej przez sito zostaje przelany do ogrzewanego zbiornika, tam zostaje ogrzany, aż wreszcie doprowadzony do bębna odśrodkowego, wirującego z wielką szybkością. Przez siłę odśrodkową woda i zanieczyszczenia jako cięższe, zostają odrzucone na zewnątrz, podczas gdy olej, jako lżejszy, pozostaje pośrodku. Zwykle olej przechodzi, następnie przez filtry do wypływu, gdzie jest zbierany. Filtr użyteczny, który jest łatwo sporządzić w każdym zakładzie, jest to filtr komorowy odpowiedniej budowy.
Olej zostaje doprowadzony u góry i przepływa przez szereg komór, gdzie przy małej szybkości przepływu zostają wydzielone wszystkie zanieczyszczenia. Zanieczyszczenia mogą być odprowadzone za pomocą specjalnych kurków wypustowych. Olej oczyszczony może być czerpany przez pompkę ręczną lub przyrządy podobne z drugiego końca filtru komorowego. Doświadczenie wykazało, że ten ustrój filtrów mimo swojej prostoty jest nadzwyczaj skuteczny.
Oleje wysokowartościowe posiadają tą właściwość, że można je po należytym oczyszczeniu, można je zawsze, ponownie używać. Jednakże, jeśli występują zanieczyszczenia chemicznej natury, których nie można usunąć za pomocą powyższych sposobów oczyszczania, to należy przede wszystkim odszukać przyczynę powstawania tych zanieczyszczeń i należy postarać się o jej usunięcie.
Kotłownia
Kotłownia i wytwarzanie pary
Para, źródło siły maszyny parowej, wpływa w dużym stopniu na smarowanie narządów stawidłowych i cylindra. Aby bliżej to wyjaśnić opiszemy poniżej kotłownię, której zadaniem jest wytwarzanie pary. W kotłowni ustawiony jest tzw. dwukomorowy kocioł opłomkowy, często spotykany w dużych siłowniach obok kotła stromo-rurkowego. Kotły te posiadają tą zaletę, iż przy jednakowej ilości wytwarzanej pary, wymagają mniejszej powierzchni, wymagają mniejszej powierzchni podstawowej, niż kotły parowe o dużej pojemności wody ( kotły płomienicowe ).
Czas potrzebny do rozruchu kotłów tych jest również nie długi, a prędzej osiągają one wydajności szczytowe; z drugiej strony są one bardziej czułe na zanieczyszczenia, które przy złej wodzie zasilającej dostają się do kotła. Obmurze kotła wykonane jest z cegły i z materiału ogniotrwałego ( cegła szamotowa ). Walczak z przestrzenią nadwodną C, połączony jest z dwoma komorami wodnymi A i B, pomiędzy którymi zawalcowana jest większa ilość pochyłych opłomek D.
Poziom wody w kotle musi leżeć nad najwyższymi częściami, które są jeszcze omywane przez spaliny, gdyż w wypadku przeciwnym istnieje niebezpieczeństwo rozżarzania się takich części, a stąd niebezpieczeństwo wybuchu kotła. Ścianki walczaka leżące nad zwierciadłem wody tzn. ścianki przestrzeni nad wodnej C, nigdy nie powinny być omywane przez spaliny. Te ostatnie z paleniska płyną drogą ku górze i omywają część górną opłomek D, przegrzewacz E, składający się z szeregu rur, następnie środkową część opłomek, a potem raz jeszcze zmieniając kierunek, do czego są zmuszone przez ogniotrwałe przegrody, omywają część dolną opłomek.
Siła ciągu w kotle może być regulowana przez klapy S, które często są poruszane samoczynnie przez osobne regulatory, aby wpływać na dzielność kotła, w zależności od jego obciążenia. Skoro spaliny oddały większość część swojego cieplika na wytworzenie pary, to zostają następnie użyte do podgrzewania wody zasilającej w podgrzewaczu P do 70 - 140 stopni C. Dopiero potem uchodzą one przez kanał, czopuch R, pod wpływem sztucznego ciągu dmuchawki U, przez komin na zewnątrz, o ile zawarty w nich cieplik nie ma być jeszcze w inny sposób wyzyskany.
Przez wsyp H węgiel spada na wolno poruszający się samoczynnie ruszt łańcuchowy F, wędruje przez całe spalenisko i spada jako żużel do popielnika, znajdującym się pod rusztem łańcuchowym. Za pomocą osobnego urządzenia do usuwania popiołu G, popiół i żużel przewożony zostaje w małych wywrotkach ( kolebach ) na żużlowisko. W kotłach dużych stosowane jest jako najoszczędniejsze, palenisko samoczynne, zwłaszcza że odręczne zasilanie wielkich powierzchni rusztowych, jest bardzo trudne. W mniejszych kotłach, przeciwne dziś jeszcze stosowane bywa palenie ręczne. W tych małych kotłowniach wystarcza zwykle ciąg naturalnych kominów, które w tym wypadku otrzymują wysokość niezbędną.
Krążenie wody oraz wytwarzanie pary odbywa się w sposób następujący :
Część górna opłomek, wystawiona na działanie przede wszystkim spalin gorących, pochłania największą ilość ciepła, przez co wytwarzanie tutaj pary jest najsilniejsze. Para wznosi się ku górze w przedniej części komory A i zbiera się w przestrzeni nadwodnej C kotła. Ponieważ górna część kotła nie jest tak mocno nagrzewana, a odbiór pary następuje z przestrzeni nadwodnej C, to wraz ze zmianą temperatury i cieplika wody zmienia się jej ciężar właściwy. W ten sposób wywołane zostaje krążenie wody takie, iż w tylnej skrzyni wodnej B opuszcza się ona w dół i przez nachylone opłomki, przechodzące stopniowo w parę, wznosi się ona stopniowo do góry. Z głównego zaworu przepustowego Y pobiera się parę nasyconą. skoro pracuje się parą przegrzaną należy przepuścić parę przez przegrzewacz E, omywany jeszcze przez spaliny bardzo gorące.
Para przepływa dalej przez rurę a i przewód rurowy, połączony z tą rurą przez zawór przepustowy c do maszyny. Z przyrządów należących do armatury; wymieniamy zawór bezpieczeństwa Z, szkła wodowskazowe Q i manometr. Zawór bezpieczeństwa reguluje najwyższą, dopuszczalną prężność pary i wydmuchuje przy przekroczeniu tej prężności parę przez rurę wiodącą na zewnątrz. Szkła wodowskazowe wskazują poziom wody w kotle, podczas gdy na manometrze odczytujemy prężność pary w kotle. Wzrastający skutek ( moc ) maszyny przy wyższym obciążeniu wymaga większego wytrzymania pary i dlatego większego użycia paliwa. Przy niedostatecznym zasilaniu paliwem prężność pary spada stopniowo, tak że prężność ta w końcu nie jest wystarczająca dla napędu maszyny.
Dlatego palacz powinien stale obserwować manometr i tak regulować doprowadzenie paliwa, aby utrzymać jednostajną prężność pary w kotle. Nowoczesne kotłownie posiadają często samoczynną regulację doprowadzania paliwa, która jest nastawiana w zależności od obciążenia kotła, często również od składu spalin. Przed nagrzewaniem maszyny należy przez otwarcie głównego zaworu przepustowego kotła Y możliwie ostrożnie rozgrzać główny przewód pary między zaworem Y a zaworem przepustowym maszyny c.
Rury przewodu parowego są dobrze otulone w celu zmniejszenia ochładzania pary. Zanim para dopływa do organów rozrządczych maszyny, wydziela ona w tak zwanym odwadniaczu b wodę porwaną z kotła. Odwadniacz powinien zatrzymywać w miarę możliwości również zanieczyszczenia, które dostają się razem z parą z kotła lub przegrzewacza. Na skutek zużycia pary przez maszynę ilość wody w kotle się zmniejsza i należy doprowadzać dalsze ilości wody, aby utrzymać stały poziom wody i nie dopuścić w żadnym razie, by woda opadła, aż do stykających się z gorącymi spalinami ścianek kotła.
Para, odpływająca z cylindra niskoprężnego, przechodzi przez odoliwiacz pary odlotowej f, gdzie zostaje wydzielony olej. Za pomocą zaworu przełączonego e maszyna może pracować z wolnym wydmuchem lub ze skraplaczem. Przy pracy z wolnym wydmuchem para uchodzi na zewnątrz przez rurę p, podczas gdy w razie przeciwnym para odlotowa zostaje skroplona w skraplaczu G. Skropliny doprowadzane są do wieży chłodzącej i mogą być ponownie zużyte do zasilania kotła. Zasilanie odbywa się za pomocą pompy do zasilania kotła N, ssącej wodę ze zbiornika i tłoczącej ją do kotła przez podgrzewacz P i zawór zasilający q.
Oprócz tego przepisane są jeszcze wbudowane urządzenia do bezpośredniego zasilania kotła wodą świeżą. Woda chłodząca, potrzebna do skraplacza, zostaje w tym wypadku zassana ze zbiornika m przez działanie próżni w skraplaczu. Po pobraniu ciepła pary odlotowej woda ta, już ogrzana, zostaje odprowadzana przez rurę wylewną k przy pomocy tzw. pompy próżniowej mokrej h, ( napędzanej w tym wypadku przez dźwignię ) do wieży chłodzącej gdzie rozpryskuje się na kropelki, zbiera się znów w zbiorniku m, zaś opadając, oddaje swój cieplik powietrzu. Chłodzenie wody przy pomocy urządzenia do chłodzenia powrotnego z wieżą chłodzącą daje się ominąć, skoro zakład przemysłowy posiada wodę bieżącą w ilości dostatecznej.
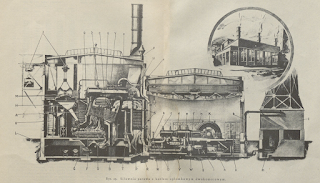 |
Siłownia parowa z kotłem opłomkowym dwukomorowym |
A - Przednia komora wodna, B- Tylna komora wodna, C - Walczak, D- Opłomki, E - Przegrzewacz, F- Ruszt łańcuchowy, G - Urządzenie do usuwania popiołu, H - Wsyp węgla, J - Kolejka węglowa, K - Urządzenie do zmiękczania wody, L - Przewód rurowy do wody zasilającej, M - Przewód smoczkowy, N - Pompa zasilająca kocioł, O - Rura ssąca do wody zasilającej, P - Podgrzewacz wody zasilającej, Q - Wodowskaz, R - Czopuch komina, S - klapy zamykające, T - Kanał okrężny, U - Urządzenie sztucznego ciągu, V- Cylinder wysokoprężny, W - Cylinder niskoprężny, X - Prądnica, Y - Główny zawór przepustowy, Z - Zawór bezpieczeństwa, a - Główny przewód pary, b - Odwadniacz, c - główny zawór przepustowy maszyny, d - Przelotnia, e - Zawór przełączony, f - Odoliwiacz, g - Skraplacz, h - Pompa próżniowa mokra, i - Pompa do wody chłodzącej, k - Rura wylewna dla skroplin, l - wieża chłodząca, m - Zbiornik wody, n - Tablica rozdzielcza, o - Zbiornik oleju odzyskanego, p - Rura wydmuchowa, q - Zawór zasilający.